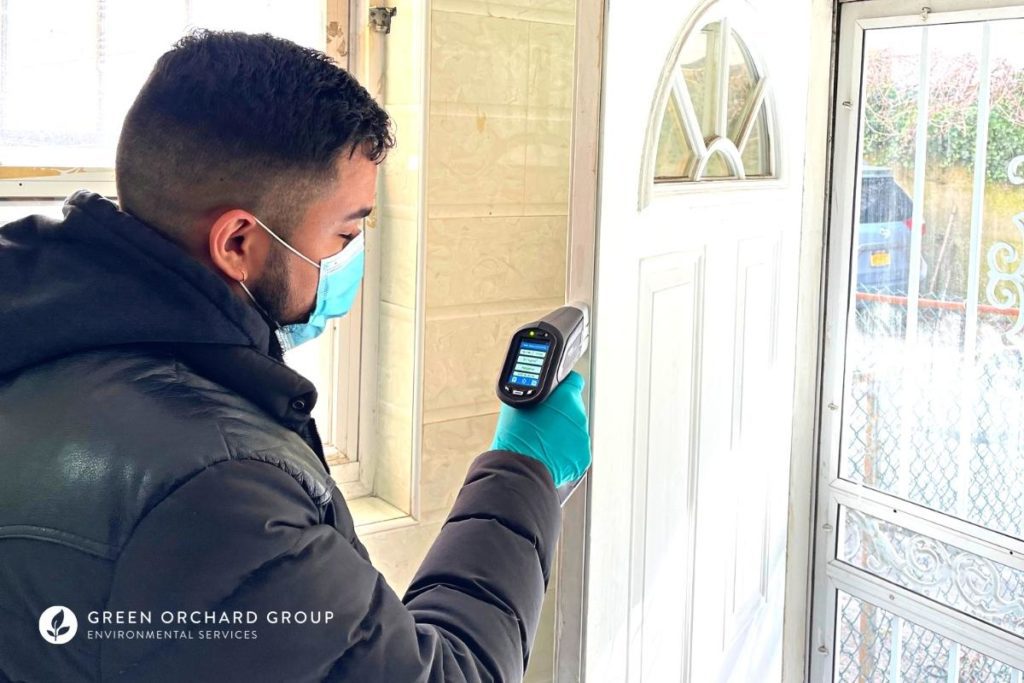
Jump to Section:
X-Ray Fluorescence (XRF) analysis is a proven technology used to detect and quantify the amount of lead present in old paint.
XRF lead testing is required for pre-1978 residential buildings in New York City, per Local Law 31.
EPA-certified lead inspectors use handheld XRF analyzer machines, which resemble radar guns, to accurately test all types of surfaces for the presence of lead-based paint.
The advantage of XRF inspections is that this method is non-destructive (no need to remove and collect samples) and the analyzer can detect lead-based paint even when it’s buried underneath multiple layers of paint.
When Is XRF Lead Paint Testing Required?
Local Law 31 of 2020 applies to owners of buildings built before 1960 (or between 1960ā1978 if the owner knows there is lead-based paint). It requires:
- XRF lead testing for all tenant-occupied dwelling units and common areas, which must be performed by an EPA-certified lead inspector or risk assessor using approved XRF analyzers.
- The inspections must be completed within 5 years (by August 2025).
- If a child under 6 resides or moves into an apartment, the unit must be inspected within 1 year.
- Copies of records for completing lead testing requirements must be maintained for 10 years.
Failure to comply with these requirements and deadlines will result in a Class āCā hazardous violation. Property owners will be liable for civil penalties of $1,000 minimum and $5,000 maximum per violation.
XRF inspections are also required if you wish to apply for an HPD lead exemption (Lead Free or Lead Safe). You can learn more about applying for lead exemptions here.
Certified XRF Lead Inspections in NYC
Green Orchard Group is an EPA-certified lead inspection firm in New York City with over 25 years of experience. Call (212) 218-8261 or fill out the form to request a free quote.
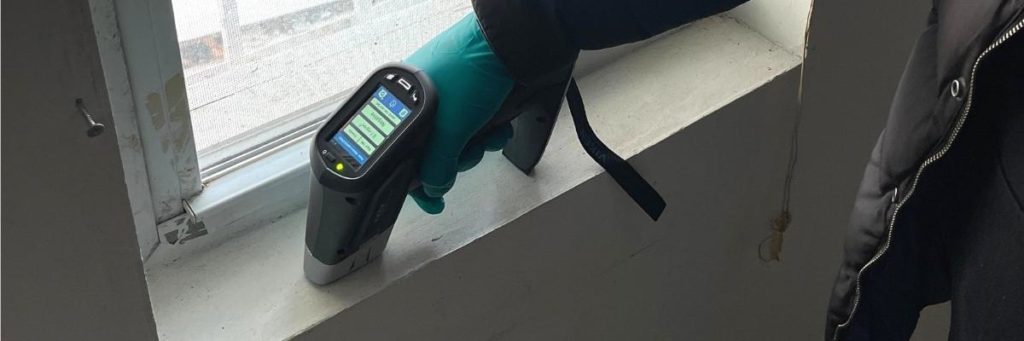
How X-Ray Fluorescence (XRF) Works
X-Ray Fluorescence (XRF) is a method of determining the elemental composition of materials. When it comes to housing and environmental safety, professionals use XRF analyzers specifically to measure the concentration of elemental lead in old paint.
This method fires x-ray beams at a paint sample to “knock” electrons out of orbit. When this happens, a certain amount of energy is released ā this energy is unique to each element. The XRF analyzer detects these individual bursts of energy to calculate how much of each element is present within the sample.
XRF is the only reliable, non-destructive technique for testing lead-based paint. Because x-rays easily penetrate the surface of paint samples, XRF analysis can detect traces of lead even when buried under multiple layers of paint.
That means it doesn’t require removing samples in order to take measurements, nor does it require marking or damaging the surface (which can potentially release dangerous lead dust).
With handheld XRF analyzers, each measurement only takes a matter of seconds and allows lead inspectors to quickly and safely test a large number of paint surfaces in a relatively short amount of time.
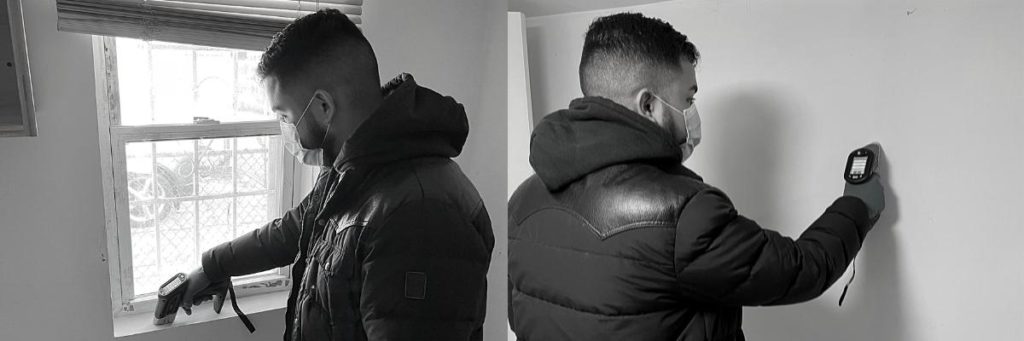
The XRF Lead Testing Process
In order to comply with Local Law 31, XRF lead testing must be performed by an EPA-certified lead inspector or risk assessor.
XRF lead testing involves a surface-by-surface investigation to determine whether lead-based paint is present in a house, dwelling unit, or residential building. The inspector holds the XRF analyzer directly on each painted surface in order to take measurements, which are then classified based on EPA / HUD standards.
Per Local Law 66, if the measurement is greater or equal to 0.5 milligrams per square centimeter (mg/cm2), it is classified as a positive reading for lead-based paint.
Sometimes readings may be considered inconclusive if they fall within a certain range, as specified by the manufacturer’s Performance Characteristic Sheet (PCS) for each model of XRF lead-based paint analyzer. In such a case, or if XRF readings cannot be taken because some surfaces are uneven or damaged, paint chip samples must be collected and analyzed in an accredited laboratory.
After the inspection is completed, you will receive an inspection report documenting all findings. Per HUD guidelines, the report should contain the following information:
- Who performed the inspection
- Date(s)
- EPA certification number of the inspector
- All XRF readings
- Classification of all surfaces as positive or negative
- Specific information on the XRF and laboratory methodologies
- Housing unit and sampling location identifiers
- Results of any laboratory analyses
- Summary of disclosure requirements based on whether or not lead-based paint was found
Random Statistical Sampling for Multi-Family Housing
HUD’s guidelines allow for the use of a random sampling protocol to test for lead-based paint in large, multi-family housing buildings.
Instead of testing each individual dwelling unit, the inspector will perform XRF lead testing only on a fraction of the total units. The fraction is determined based on the date of the building’s construction (pre-1960 or 1960-1977) and the total number of units in the building.
This method is generally less time-consuming and more cost-effective for large housing buildings, although there are certain drawbacks (such as when you’re applying for an HPD lead exemption).
About Green Orchard Group
Looking for reliable, EPA-certified XRF lead testing in New York City? Green Orchard Group is here to help!
We have over 25 years of experience helping NYC building owners and landlords with professional lead inspection and abatement services. Our lead experts work closely with our contacts at HPD and the Department of Health to guarantee the highest level of compliance with city regulations and standards.
Call (212) 219-8261 or click below to contact us today if you have questions about Local Law 31 testing requirements or need help scheduling an XRF lead testing inspection.